Industrial cleaning of metals is a very important (and sometimes underestimated) step in ensuring that a component performs the function for which it has been designed, contributing to the efficient and long-lasting operation of the system of which it is a part. This article gives an overview of the main cleaning processes available, the technologies currently on the market, and the sectors in which they are applied.
Industrial cleaning processes remove contaminants such as machining oils, lubricants, or scrap left by the mechanical processing operations carried out on a metal workpiece. If these contaminants are not perfectly removed, there is a risk that problems will arise during the subsequent processing, finishing, or assembly stages, compromising the quality of the component and, ultimately, of the system of which it is part.
Industrial cleaning of metals: methods and processes, and how to choose them
Industrial cleaning operations are carried out manually or, more and more often, with automated machines that can effectively remove both machining oils and swarf or chips.
Typically, a cleaning process uses water-based or solvent-based products and it consists of four steps – pre-cleaning, cleaning, rinsing, and drying – that can be customised to suit individual requirements. Moreover, different types of operation can be employed and combined with each other, i.e. spray, immersion, ultrasonic, vacuum, dry, injection, and high-pressure cleaning.
An HMI display for managing a cleaning cycle.Cleaning machines can treat both small parts and large parts. Therefore, the size of the plant (and thus of the cleaning chamber) and the greater or lesser number of parts treated per cycle vary depending on the type of process required.
New generation machines are normally designed in line with the Industry 4.0 principles, in order to be integrated into the existing production lines and to interface with the company’s management systems, making it possible to monitor process parameters. In addition, they allow pre-setting different cleaning programmes, which can be selected according to the material and shape of the parts to be treated, thus enabling to adjust the duration of the cycle, the temperature, the movement of the basket, the possible use of ultrasound, and so on.
Although all the cleaning processes and methods mentioned above can prove efficient and effective, the choice of the most suitable technology and product for one’s own manufacturing needs should be based on three main factors:
- the material of the components to be treated,
- the type of contaminant
to be removed,
- the shape of the parts to be handled.
Our advice is to carry out tests on one’s own workpieces. Usually, this type of service is provided by the technology and product suppliers themselves, which can help identify the most suitable process for every need.
Water cleaning
Industrial water cleaning employs detergents
as the cleaning products, which exert a chemical-physical action on contaminating agents to remove them from the parts’ surfaces.
This method is considered one of the most environmentally friendly as the detergents used do not contain any volatile organic compounds (VOCs) and therefore there is no need for suction systems. In addition, many water-based cleaning machines perform closed loop operations and the liquid used during the process is recovered and recirculated to reduce water consumption.
Solvent cleaning
Solvent cleaning is usually carried out using new generation solvents with a low environmental impact, such as modified alcohols and hydrocarbons.
The latest generation of systems guarantees continuous distillation of the cleaning product, which therefore remains stable and effective over time. In addition, the use of solvents is usually kept to a minimum and their disposal does not require any special treatment, as they are non-hazardous.
How to ensure effective cleaning
Workpiece positioning and basket movement
Depending on their type, the parts to be treated can be either placed in bulk in the cleaning basket, as is often the case with small components, or installed on special fixtures designed to guarantee the best results, for example in the case of large hydraulic components or particularly delicate workpieces that could be damaged by bumping into each other.
Besides the parts’ arrangement, another factor that determines a process’ effectiveness is the combined action of the cleaning product and the movement of the basket. In fact, a cleaning operation can be static or dynamic. In the latter case, the basket can tilt or rotate, even 360 degrees. Again, the choice depends on the characteristics of the parts to be treated and the type of contaminant to be removed.
The use of ultrasound
Out of the different methods mentioned at the beginning of this article, one innovative technology that is increasingly being combined with vacuum, spray, or immersion processes is ultrasound.
When ultrasound is used, the chemical action of the cleaning product is combined with the mechanical action generated by high-frequency waves that create micro shock waves capable of separating the dirt from the workpieces. This physical phenomenon is called cavitation.
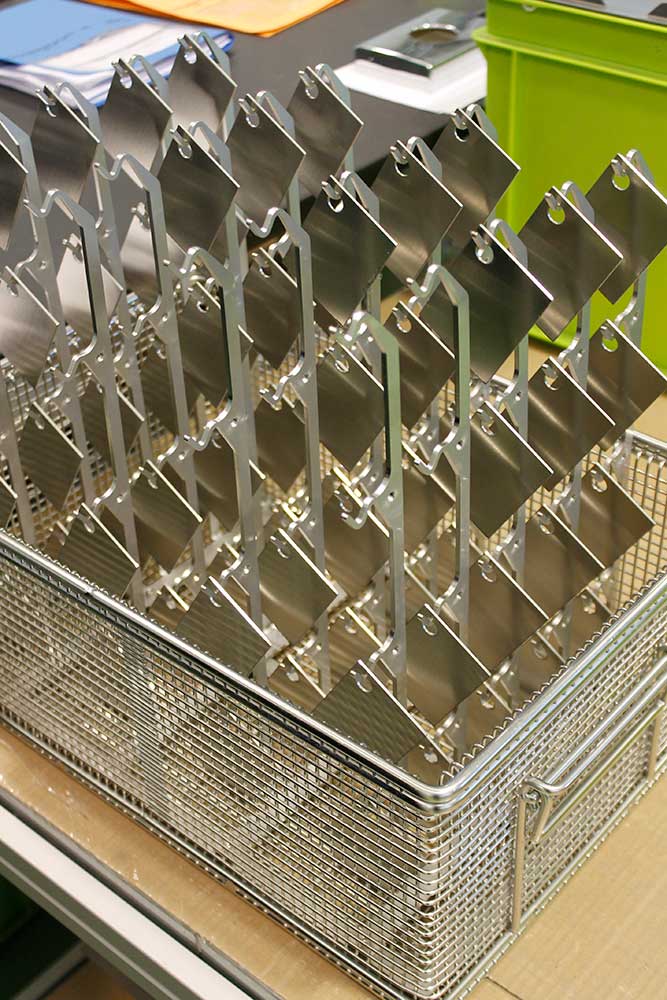
The use of ultrasound in a process tank guarantees superior cleaning quality and often offers a process advantage, especially when the parts to be cleaned feature particularly complex geometries that make it difficult to remove contaminants.
The effect of ultrasound.Fields of application
As already mentioned, the industrial cleaning stage is of fundamental importance to ensure the quality and correct functioning of a product.
Every part subjected to mechanical processing requires a certain cleanliness degree. Therefore, industrial cleaning technologies are widely used in the production processes of hydraulic, hydropneumatic, and electromechanical components, gearmotors, pumps, small metal parts such as screws and bolts, fashion accessories, eyewear, medical instruments, car components, bathroom fittings and accessories, and moulds.
The ICT_Industrial Cleaning Technologies magazine brings together articles about all these sectors, as well as in-depth reports covering all aspects of industrial cleaning and cleaning control processes, industry news, and market overviews. You can browse through all published issues and subscribe to the digital version free of charge.