In just nine months, Dürr built a new smart and eco-friendly paint shop for the Chinese electric vehicles manufacturer SERES.
Dürr has recently announced that it has concluded the installation of a new smart and sustainable coating plant for SERES. Founded in 2018, SERES is a Chinese
manufacturer of electric vehicles shipping its products to over seventy countries that requested Dürr to design and build a new coating plant capable of completing sixty painting operations per hour for its Liangjiang site in Chongqing (southwestern China). The Germany engineering company has developed a modular structure that allowed to efficiently complete the project in just nine months
– from receipt of the contract to the start of production
The layout of the individual modules such as pretreatment, sealing processes, paint booths and ovens ensures a more flexible production and eliminates unused space within the paint shop. Furthermore, in response to a specific request of the client, Dürr also factored in space for a future primer line within the layout.
The plant includes the RoDip® M mechanical rotational process, a 360° rotational movement which spins the bodies around their own axes, eliminating the need for an inclined exit section in the immersion tanks. It then allows to save up to six meters in length per tank compared to pendulum conveyor technology, reducing water, chemical and energy usage.
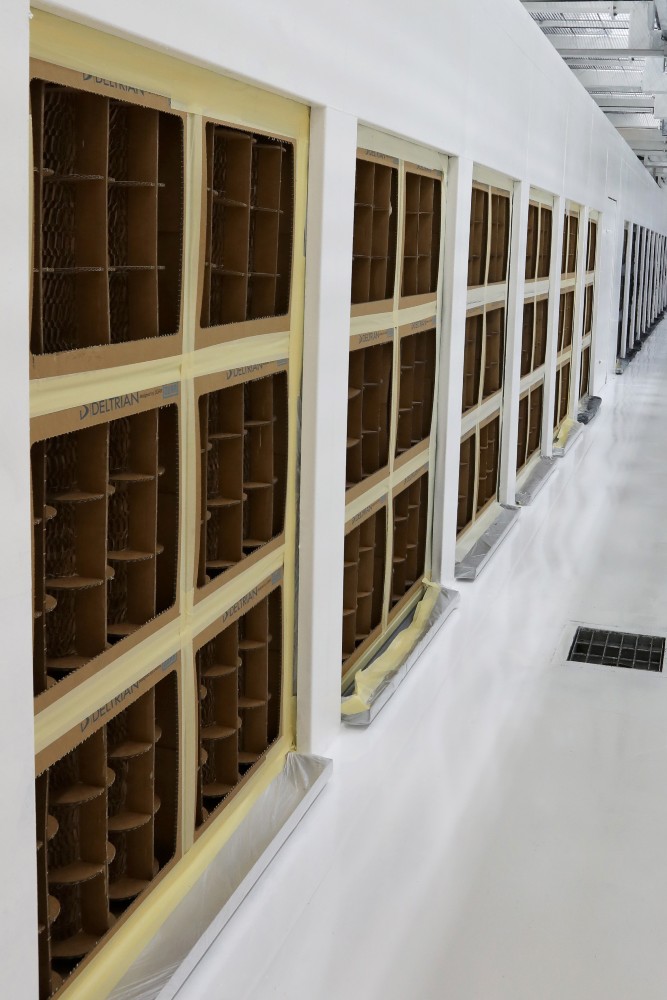
In order to remove the overspray, the line will be equipped with the EcoDry X dry separation system
that relies on easily replaceable disposable cardboard filters, eliminating the need for water and chemicals. As a matter of fact, dry separation minimises fresh air requirements by recirculating nearly 90% percent of the air.
Moreover, to eliminate solvents and volatile organic compounds from the exhaust air, which has already undergone adsorptive concentration through the recirculation process, the paint booths are equipped with a compact air pollution control system in combination with the downstream Oxi.X TR TAR recuperative thermal oxidizer. Additionally, exhaust air from the ovens is purified via the integrated Oxi.X TR TAR afterburning system with heat recovery and then reintroduced into the oven heating system, reducing energy consumption by 15%.
Finally, the sustainability of the new paint shop of SERES is enhanced by the DXQcontrol software family for higher-level plant control, seamlessly tracking the life-cycle of each car body. The DXQenergy.management tool provides a transparent overview of energy and media consumption across the entire production plant or for specific areas, while the DXQequipment.maintenance monitors when individual components like pumps, valves or filters need to be maintained.
“To meet the requirements of a production process that saves both resources and energy, we used especially sustainable products from plant and environmental engineering and installed our DXQ energy management solution. We are very happy that we were able to impress SERES with our modular equipment and fast completion time, and look forward to a long-term partnership,” has explained Yu Lin, the vice-president of the paint and final assembly business of Dürr China.