The EcoQPower energy flow management system of Dürr increased the energy efficiency of the paint shop of a car manufacturer.
The German engineering company Dürr has recently announced that it has provided a German car manufacturer with its new EcoQPower energy flow management system, that allowed it to reduce the total energy consumption of its paint shop by 19%.
EcoQPower allows plant operators to move away from gas and fossil fuels, towards a climate-neutral production process through electrification. The system is based on a comprehensive analysis of the individual heating and cooling requirements of the paint shop, increasing them substantially and ensuring that no energy is left unused by intelligently networking all components.
Instead of optimising individual elements, the system considers the paint shop collectively, including the energy input of the plant. In order to get the most from all available energy sources, the energy flows for the supply of all the equipment and processes are networked: instead of supplying each process area – for example the paint booths or the pretreatment zone – individually, each process area only receives the exact amount of energy it needs to operate efficiently and to reach the required temperature level, making it possible to exploit waste heat sources that previously went unused.
As a matter of fact, Dürr has developed a software that determines heating and cooling requirements in the form of a source/sink profile that considers the climatic site conditions and general framework data, such as production capacities, vehicle types and the available energy sources which can be incorporated. Recognising which waste heat sources can be used for what makes it possible to take advantage of synergies from the processes and to select and exactly size the right hardware components for the intended purpose, whether heat pumps, hot and cold water tanks, or a cooling tower.
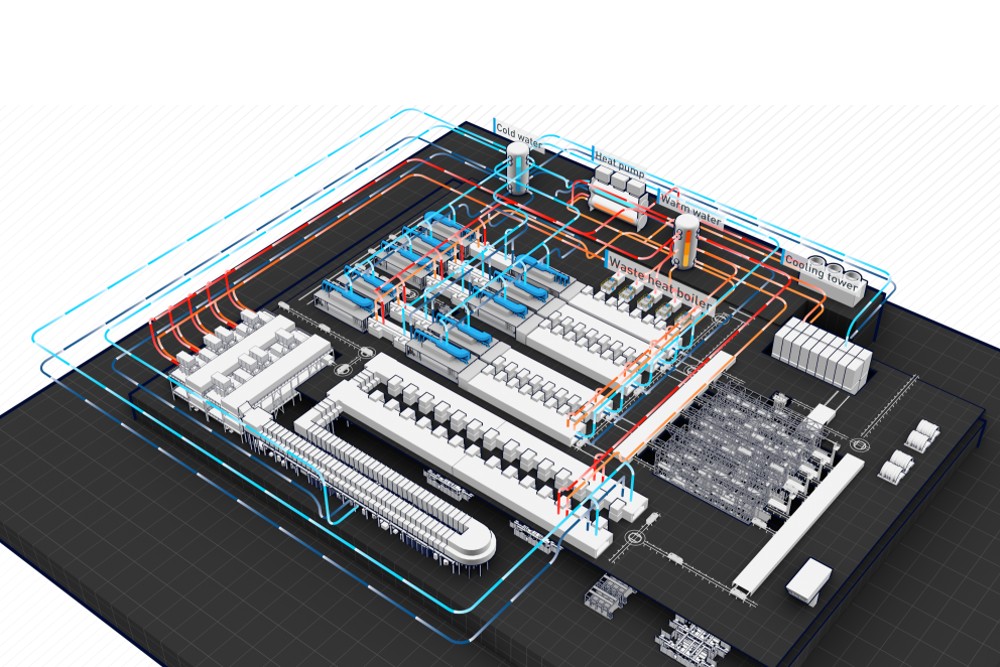
EcoQPower also takes a different approach to energy supply, which until now was centrally organised for car plants. For optimal energy solutions, the cold and heat are generated de-centrally within the paint shop using electricity, recovered and distributed yet again to the components via intelligent networking.
“EcoQPower is a milestone in energy efficiency. Even in climatically ideal locations for paint shop operation, we are achieving energy savings in the double-digit percentage range. This is equivalent to the amount of energy needed to paint 13,000 to 20,000 cars,” has stated Dietmar Wieland, the senior manager of research and development at Dürr. “EcoQPower improves each new plant’s energy efficiency, mostly in combination with specific energy-saving products, such as our electric oven EcoInCure and the electric exhaust air purification system Oxi.X RV. We are using these in our first project with EcoQPower in a new, fully electrified paint shop for a German car manufacturer. In doing so, we are minimizing energy consumption so significantly that it offsets most of the additional costs of switching to this more expensive energy source of electricity.”